Key Takeaways
- MakinaRocks is an AI-powered predictive maintenance solution designed for industrial operations.
- It leverages machine learning and data analytics to reduce downtime and optimize equipment performance.
- The company’s mission is to enhance operational efficiency and minimize unexpected failures.
Industries like manufacturing, energy, and logistics benefit from its advanced anomaly detection and predictive insights.
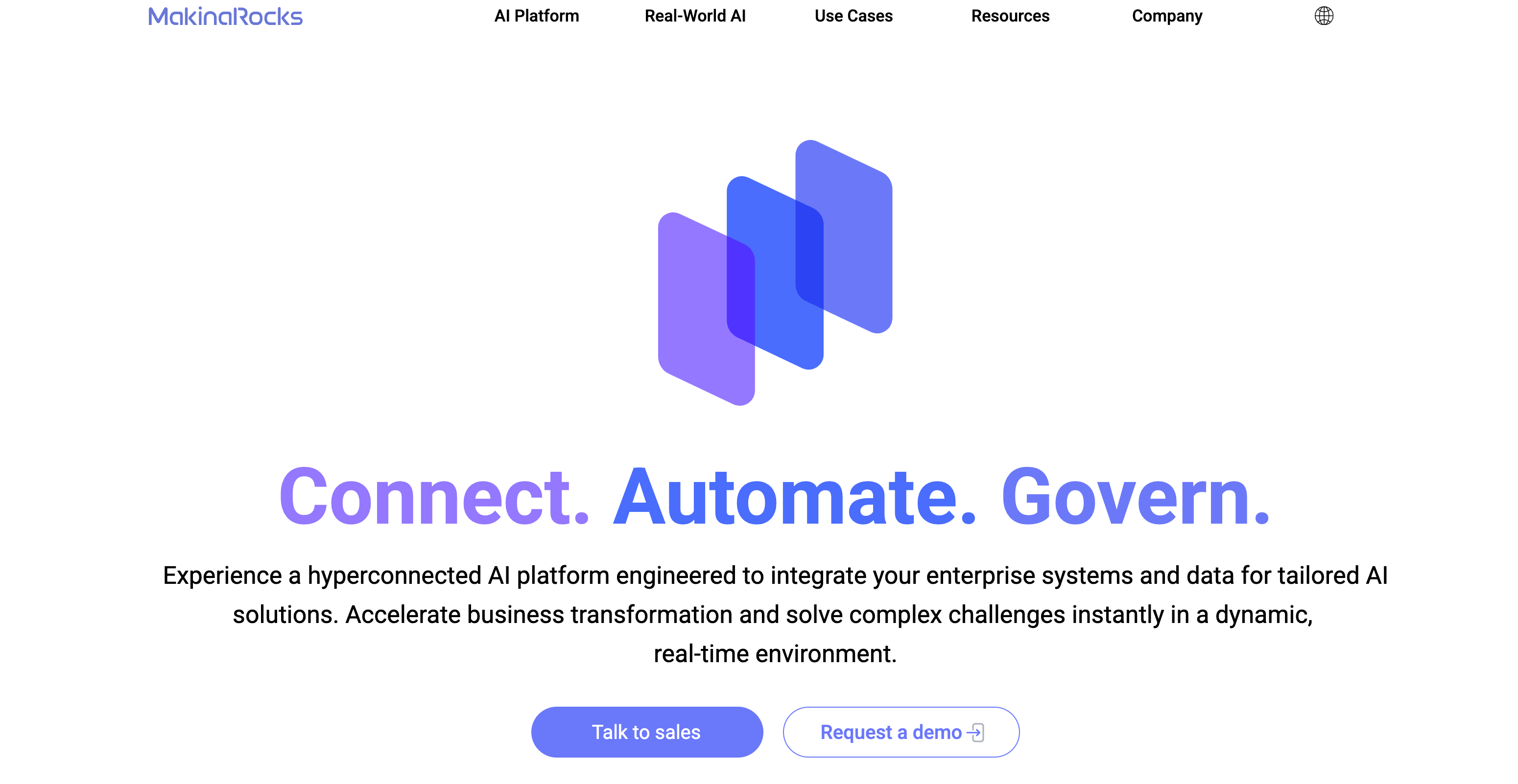
Introduction to MakinaRocks
Predictive maintenance is revolutionizing industrial operations, helping businesses cut costs, improve efficiency, and prevent equipment failures before they happen.
At the forefront of this transformation is MakinaRocks, an AI-driven solution that uses machine learning to optimize maintenance strategies.
If you’re managing industrial machinery, you know the challenges of unexpected breakdowns. A single unplanned outage can disrupt production, increase operational costs, and lead to revenue loss. Traditional maintenance strategies—like scheduled inspections—are often inefficient, either causing unnecessary downtime or missing hidden issues.
This is where MakinaRocks stands out. By combining AI, machine learning, and big data analytics, the platform helps businesses transition from reactive maintenance to a proactive, predictive approach. Companies using MakinaRocks can detect anomalies, forecast failures, and extend equipment lifespan, all while reducing costs.
But what exactly is MakinaRocks, and how is it shaping the future of predictive maintenance? Let’s dive deeper into its purpose, mission, and impact on industrial operations.
What is MakinaRocks?
MakinaRocks is a Seoul-based AI-driven startup specializing in predictive maintenance and anomaly detection for industrial applications. Founded with the goal of optimizing operations across various industries, the company leverages advanced machine learning models to analyze equipment data and predict potential failures before they occur.
Unlike traditional maintenance solutions that rely on fixed schedules, MakinaRocks applies self-learning AI algorithms to monitor real-time equipment performance. These models identify subtle patterns in data that might indicate potential failures, helping businesses reduce downtime, increase efficiency, and improve overall operational reliability.
With industries such as manufacturing, energy, and logistics relying heavily on complex machinery, MakinaRocks provides a data-driven approach to keep operations running smoothly. Its technology adapts to different equipment types, ensuring that maintenance strategies are tailored to the unique needs of each business.
The Purpose and Mission of MakinaRocks
MakinaRocks was founded with a clear mission: to revolutionize industrial maintenance through AI-driven innovation. The company aims to replace outdated maintenance models with intelligent, predictive solutions that help businesses stay ahead of equipment failures.
At its core, MakinaRocks is dedicated to:
- Reducing unplanned downtime – By predicting failures before they happen, businesses can avoid costly disruptions.
- Improving asset longevity – AI-driven insights enable better maintenance decisions, extending the life of industrial equipment.
- Enhancing operational efficiency – Smarter maintenance reduces waste, optimizes production schedules, and improves resource allocation.
- Minimizing costs – Proactive maintenance prevents unnecessary repairs and reduces overall maintenance expenses.
By integrating AI, IoT, and real-time analytics, MakinaRocks empowers industrial companies to shift from reactive to predictive maintenance. This not only helps improve operational efficiency but also supports sustainability efforts by reducing waste and energy consumption.
With an increasing number of industries embracing digital transformation, MakinaRocks is at the forefront of predictive maintenance, providing businesses with the tools they need to optimize operations and prevent costly failures.
Key Features of MakinaRocks
MakinaRocks is redefining predictive maintenance with its AI-powered solutions. By leveraging machine learning, deep learning, and real-time data analytics, the platform provides industrial businesses with unparalleled insights into equipment health and performance.
Here’s a breakdown of its core features and how they enhance operational efficiency:
1. AI-Powered Anomaly Detection
Traditional monitoring systems often fail to detect early-stage faults. MakinaRocks’ AI-driven anomaly detection continuously analyzes sensor data, identifying subtle deviations in equipment behavior. This allows businesses to catch potential failures before they escalate, reducing unplanned downtime.
2. Predictive Failure Analysis
Using historical and real-time data, MakinaRocks predicts when equipment is likely to fail. Its predictive failure analysis helps businesses schedule maintenance at the right time, avoiding unnecessary repairs while ensuring reliability.
3. Self-Learning Algorithms
One of MakinaRocks’ standout features is its adaptive AI models. These self-learning algorithms evolve over time, becoming more accurate as they process more data. This means continuous improvement in maintenance strategies without the need for constant human intervention.
4. Scalable Integration
MakinaRocks is designed to integrate seamlessly into existing industrial IoT (IIoT) and manufacturing execution systems (MES). Whether you’re operating a small-scale plant or a large enterprise, its flexible architecture ensures easy deployment across different environments.
5. Real-Time Monitoring & Alerts
With real-time data streaming, MakinaRocks enables businesses to monitor asset health 24/7. It provides instant alerts when anomalies are detected, allowing maintenance teams to take immediate action before failures occur.
6. Data-Driven Maintenance Optimization
Instead of following rigid maintenance schedules, companies can use data-driven insights to optimize their maintenance strategies. MakinaRocks provides recommendations based on actual equipment conditions, helping businesses save costs and maximize uptime.
Advanced Manufacturing Solutions
In the manufacturing industry, even a minor machine failure can disrupt entire production lines, leading to delays and financial losses.
MakinaRocks addresses this challenge by providing AI-driven predictive maintenance solutions tailored for modern manufacturing needs.
- Reducing Downtime in Smart Factories
Smart factories rely on automated machinery and robotics, making predictive maintenance crucial. MakinaRocks monitors equipment in real time, identifying performance irregularities and reducing unplanned stoppages.
- Optimizing Production Efficiency
By using machine learning models, MakinaRocks helps manufacturers optimize workflows. It ensures that machines operate at peak efficiency, preventing performance degradation and reducing energy consumption.
- Extending Machine Lifespan
Regular predictive insights allow manufacturers to extend the lifespan of expensive machinery. This reduces capital expenditures on new equipment, improving the overall return on investment (ROI).
Industry Applications of MakinaRocks
MakinaRocks’ technology isn’t limited to just manufacturing. It plays a vital role across multiple industries, helping businesses maintain reliability and efficiency.
1. Energy Sector
In power plants and renewable energy facilities, equipment reliability is critical. MakinaRocks predicts failures in turbines, transformers, and generators, ensuring uninterrupted energy supply and reducing costly shutdowns.
2. Logistics & Transportation
From automated warehouses to fleet management, MakinaRocks ensures that machinery and vehicles operate efficiently. By detecting anomalies in conveyor belts, cranes, and delivery trucks, it prevents unexpected failures that could disrupt supply chains.
3. Aerospace & Defense
Aircraft and defense systems require high-precision maintenance. MakinaRocks’ predictive analytics help detect early-stage wear and tear in aircraft components, improving safety and reducing maintenance costs.
4. Semiconductor & Electronics Manufacturing
Semiconductor fabrication plants rely on ultra-precise machinery. MakinaRocks ensures optimal performance of chip-making equipment, preventing costly defects and maintaining high production quality.
By integrating AI with real-time equipment monitoring, MakinaRocks is transforming predictive maintenance across industries. It’s not just about preventing failures—it’s about unlocking new levels of operational efficiency.
Benefits of Using MakinaRocks
Adopting MakinaRocks for predictive maintenance goes beyond just preventing equipment failures—it’s about transforming how businesses manage their operations. From cost savings to improved efficiency, the platform helps industrial companies stay competitive in a fast-evolving landscape.
1. Efficiency & Cost Savings
One of the biggest advantages of MakinaRocks is its ability to reduce operational costs while improving efficiency. Traditional maintenance approaches often lead to unnecessary repairs or unexpected failures, both of which drive up expenses. With AI-driven predictive maintenance, businesses can:
- Minimize unplanned downtime, preventing production losses.
- Extend equipment lifespan, reducing capital expenditures on new machinery.
- Optimize resource allocation, ensuring maintenance teams focus on critical issues rather than routine checkups.
For industries like manufacturing, energy, and logistics, where downtime can cost millions, these savings are game-changing.
2. Enhanced Production Quality
When machines operate at peak performance, product quality improves. MakinaRocks helps maintain optimal production conditions by:
- Detecting anomalies that could impact product consistency.
- Reducing defects caused by misaligned or malfunctioning equipment.
- Ensuring stable production environments, leading to fewer errors and higher customer satisfaction.
For industries like semiconductor manufacturing or aerospace, where precision is critical, this translates into higher yield rates and reduced waste.
3. Scalability and Flexibility
MakinaRocks is built to adapt to different industries and operational scales. Whether a business operates a single factory or multiple global facilities, the platform provides:
- Seamless integration with existing industrial IoT (IIoT) systems.
- Customizable AI models that evolve based on specific equipment and industry needs.
- Cloud-based or on-premise deployment options, catering to different IT infrastructures.
This flexibility ensures that companies of all sizes can leverage predictive maintenance without major system overhauls, making MakinaRocks a future-proof solution for industrial efficiency.
Getting Started with MakinaRocks
Adopting MakinaRocks for predictive maintenance is a strategic move toward improving efficiency and reducing operational risks. But how do you implement it effectively? The process is straightforward, ensuring businesses can integrate AI-driven maintenance without disrupting ongoing operations.
Step-by-Step Guide to Implementing MakinaRocks
1. Assess Current Maintenance Strategy
Before implementing MakinaRocks, businesses must analyze existing maintenance workflows. This involves identifying pain points, such as frequent equipment failures, excessive downtime, or inefficient maintenance schedules.
2. Data Collection & Integration
MakinaRocks requires real-time and historical equipment data to function effectively. Businesses need to:
- Integrate IoT sensors (if not already in place) for continuous data monitoring.
- Connect existing industrial IoT (IIoT) or manufacturing execution systems (MES) to MakinaRocks.
- Ensure data is structured and accessible for AI-driven analysis.
3. AI Model Training & Customization
Unlike traditional maintenance software, MakinaRocks uses self-learning AI models. The system:
- Analyzes historical data to understand equipment behavior patterns.
- Identifies early signs of failures by detecting anomalies in performance data.
- Customizes predictive models based on specific machinery and industry needs.
4. Testing & Pilot Deployment
Before a full-scale rollout, businesses can deploy MakinaRocks in a pilot phase to evaluate its effectiveness. During this phase:
- The system fine-tunes its predictive capabilities based on real-time feedback.
- Maintenance teams validate alerts and AI-generated insights.
- Adjustments are made to optimize accuracy and response strategies.
5. Full Deployment & Continuous Improvement
Once validated, MakinaRocks is deployed across all critical assets. The system continuously learns and improves, ensuring that predictive maintenance strategies evolve with changing operational needs.
With real-time monitoring, automated alerts, and AI-driven maintenance insights, businesses gain complete control over equipment reliability and uptime.
Case Studies and Success Stories
Several industrial giants have already leveraged MakinaRocks to optimize their maintenance processes. Here are some standout implementations:
1. Smart Manufacturing – AI-Powered Predictive Maintenance
A leading semiconductor manufacturer integrated MakinaRocks to monitor high-precision machinery. Before implementation, unexpected equipment failures caused production losses worth millions. After deploying MakinaRocks’ AI models, the company:
- Reduced downtime by 40% through early fault detection.
- Improved chip yield rates by identifying defects before production failures occurred.
- Achieved significant cost savings by optimizing maintenance schedules.
2. Energy Sector – Preventing Power Grid Failures
A major energy provider faced frequent power transformer failures, leading to service disruptions and expensive emergency repairs. With MakinaRocks, they:
- Identified early warning signs in transformers before failures occurred.
- Reduced maintenance costs by 30% by shifting from reactive to predictive maintenance.
- Ensured uninterrupted power supply to critical regions, improving service reliability.
3. Logistics & Transportation – Fleet Maintenance Optimization
A global logistics company managing a fleet of automated vehicles implemented MakinaRocks to enhance fleet reliability. The results:
- Reduced vehicle breakdowns by 50%, preventing delivery delays.
- Optimized fuel efficiency and maintenance schedules through AI-driven insights.
- Increased overall supply chain efficiency, leading to faster delivery times.
These success stories highlight MakinaRocks’ impact across different industries, proving that AI-driven predictive maintenance is the future of industrial efficiency.
Challenges and Solutions in Using MakinaRocks
Common Challenges in Implementation
While MakinaRocks offers cutting-edge predictive maintenance solutions, businesses may encounter a few hurdles during implementation, such as:
- Data Availability & Quality – Inconsistent or incomplete historical data can limit AI model accuracy.
- Integration Complexity – Connecting MakinaRocks with legacy systems or existing IoT platforms may require additional configurations.
- Workforce Adaptation – Employees might resist AI-driven maintenance due to a lack of familiarity or fear of automation replacing jobs.
Solutions and Best Practices
- Ensure Comprehensive Data Collection – Install IoT sensors where necessary and structure existing data for better AI model training.
- Use a Phased Integration Approach – Start with a pilot program before a full-scale rollout, allowing gradual adaptation.
- Train and Upskill Teams – Conduct workshops and hands-on training to help employees understand and utilize MakinaRocks effectively.
With the right strategy, businesses can seamlessly integrate MakinaRocks and unlock its full potential.
Future of Manufacturing with MakinaRocks
Trends Shaping the Future
The manufacturing industry is rapidly evolving, with AI and IoT playing a central role. Predictive maintenance is no longer optional—it’s a necessity for maintaining a competitive edge. Key trends include:
- AI-driven Smart Factories – More manufacturers are shifting to fully automated and predictive production lines.
- Sustainable Manufacturing – AI-powered efficiency helps reduce energy consumption and waste, supporting green initiatives.
- Digital Twins Technology – MakinaRocks can integrate with virtual factory simulations, improving real-time decision-making.
Innovation and Development at MakinaRocks
MakinaRocks continues to invest in AI research, advanced analytics, and scalable integration, ensuring that manufacturers stay ahead of technological disruptions. With customizable AI models and real-time adaptability, it remains a leader in predictive maintenance.
Conclusion: Why Choose MakinaRocks?
MakinaRocks is more than just a predictive maintenance tool—it’s a game-changer for industrial efficiency. By leveraging AI, machine learning, and real-time analytics, businesses can:
- Reduce downtime and prevent costly failures.
- Optimize maintenance strategies for long-term savings.
- Enhance production quality through data-driven insights.
For businesses looking to embrace the future of manufacturing, MakinaRocks is the ultimate AI-powered solution.
FAQs
1. What industries can benefit from MakinaRocks?
MakinaRocks is designed for industries that rely on complex machinery and automated systems, including:
- Manufacturing – Reducing downtime and improving production efficiency.
- Energy & Utilities – Ensuring uninterrupted power supply and grid stability.
- Logistics & Transportation – Enhancing fleet reliability and supply chain operations.
- Aerospace & Defense – Preventing unexpected failures in high-precision machinery.
- Semiconductor Production – Minimizing defects and optimizing chip-making equipment.
2. How does MakinaRocks improve manufacturing efficiency?
MakinaRocks enhances efficiency by:
- Predicting equipment failures before they happen, reducing unplanned stoppages.
- Optimizing maintenance schedules, ensuring machines are serviced at the right time.
- Providing real-time insights, allowing quick decision-making for production adjustments.
- Improving product quality, reducing waste and rework costs.
3. What are the costs associated with implementing MakinaRocks?
The cost of implementing MakinaRocks depends on:
- The size of the operation – Larger facilities with extensive machinery may require a more complex setup.
- Integration needs – Compatibility with existing IoT sensors, MES, or ERP systems may affect costs.
- Customization – AI models can be tailored to specific industries, influencing pricing.
MakinaRocks offers scalable pricing options, ensuring businesses of all sizes can benefit from predictive maintenance.
4. Is there a support system in place for new users of MakinaRocks?
Yes, MakinaRocks provides:
- Comprehensive onboarding support, ensuring smooth integration.
- Training programs to help maintenance teams understand AI-driven workflows.
- 24/7 customer support to resolve technical issues quickly.
- Regular software updates to improve AI model accuracy and performance.
5. What differentiates MakinaRocks from other manufacturing solutions in the market?
MakinaRocks stands out due to:
- AI-driven anomaly detection – More advanced than traditional monitoring systems.
- Self-learning algorithms – Continuous improvements based on real-time data.
- Scalability – Works for small factories and large industrial operations alike.
- Industry-specific adaptability – Custom AI models tailored to different sectors.
- Seamless integration – Compatible with existing IIoT and MES platforms.
With a focus on innovation, efficiency, and cost reduction, MakinaRocks is the future of predictive maintenance for modern industries.